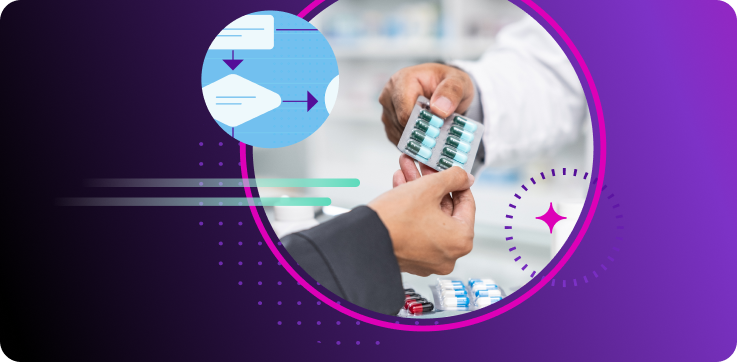
Corrective and Preventive Action (CAPA) is essential for pharmaceutical quality management. It’s a systematic process addressing product or process deviations to prevent issues, ensure product quality, and meet regulatory standards.
The goal is to prevent issues, ensure product quality, and meet regulatory standards.
In this blog post we’re going to cover the core essentials of an effective CAPA system, the importance of CAPA and critical process steps.
Core Components of CAPA
An effective CAPA process enables pharmaceutical organizations to streamline:
Deviation Identification
A CAPA process begins with recognizing product or process deviations. These can stem from various sources including customer complaints, quality control testing, internal audits, or manufacturing process monitoring. Accurate and timely identification is crucial for effective CAPA.
Investigation
Once a deviation is identified, a thorough investigation is necessary to determine the root cause. This involves collecting data, interviewing personnel, and analyzing process parameters. Tools like fishbone diagrams, 5 Whys, or failure mode and effects analysis (FMEA) can aid in root cause identification.
Corrective Action
Corrective actions address the immediate problem. These actions are implemented to prevent the recurrence of the specific deviation. Examples include reprocessing non-conforming product, implementing temporary process changes, or issuing recalls.
Preventive Action
To prevent future occurrences, preventive actions are implemented. This involves identifying and addressing the underlying causes of the problem. Examples include process modifications, equipment upgrades, or employee training.
Verification
The effectiveness of corrective and preventive actions must be verified. This involves collecting data to demonstrate that the implemented solutions have resolved the issue and prevented recurrence. Ongoing monitoring and evaluation are essential.
What’s the Big Deal about CAPA?
A good CAPA system is critical to the pharmaceutical industry. It helps ensure product quality, patient safety, regulatory compliance and more.
Regulatory Compliance
Adherence to regulatory requirements, such as those outlined by the FDA’s 21 CFR Part 820, is mandatory for pharmaceutical manufacturers. A well-structured CAPA system demonstrates a company’s commitment to quality and compliance, reducing the risk of regulatory actions.
Patient Safety
By proactively identifying and addressing product or process issues, CAPA helps prevent product defects and recalls, ultimately protecting patient safety. A strong CAPA process demonstrates a company’s dedication to patient well-being.
Product Quality
CAPA is instrumental in maintaining consistent product quality. By analyzing deviations and implementing corrective actions, companies can identify trends and implement process improvements, leading to higher quality products.
Cost Reduction
Product failures, recalls, and regulatory fines can result in significant financial losses. A proactive CAPA system helps minimize these costs by preventing issues and reducing rework.
Continuous Improvement
CAPA is an integral part of a continuous improvement culture. By analyzing trends in deviations, companies can identify opportunities to enhance processes and reduce variation.
Overview of CAPA Process Steps
Some of the critical key steps in an effective CAPA process include:
Deviation Report
A clear and concise deviation report is the first step in the CAPA process. It should include detailed information about the issue, such as date of occurrence, product or process affected, and impact on product quality or patient safety. Effective deviation reporting involves timely communication and accurate documentation.
Investigation
To identify the root cause of a deviation, a thorough investigation is necessary. This may involve collecting data, interviewing personnel, and analyzing process parameters. Tools such as fishbone diagrams or the 5 Whys method can be used to systematically explore potential causes.
Corrective Action
Once the root cause is determined, corrective actions are implemented to address the immediate problem. These actions should be specific, measurable, achievable, relevant, and time-bound (SMART). Effective corrective actions restore product or process conformance.
Preventive Action
To prevent recurrence, preventive actions are implemented. These actions address the underlying causes of the deviation and aim to improve the overall process. Examples include process modifications, equipment upgrades, or enhanced training.
Verification
The effectiveness of corrective and preventive actions must be verified through data analysis and process monitoring. This step ensures that the implemented solutions have resolved the issue and prevented recurrence.
Closure
Once the effectiveness of corrective and preventive actions has been confirmed, the CAPA process can be closed. Documentation of the entire process is essential for demonstrating compliance and facilitating continuous improvement.
The Role of Technology in CAPA
Technology plays a pivotal role in streamlining CAPA processes. By leveraging specialized CAPA software, organizations can significantly enhance efficiency and effectiveness.
Automated Workflows
CAPA software can automate routine tasks such as deviation reporting, assignment, and status updates, freeing up valuable time for investigation and analysis.
Centralized Data Repository
A centralized platform for storing and managing CAPA-related documents, records, and data ensures easy accessibility and traceability.
Efficient Collaboration
Facilitating seamless communication and collaboration among cross-functional teams involved in the CAPA process through features like task assignments, notifications, and document sharing.
Data Analytics and Reporting
Generating comprehensive reports and visualizations to identify trends, measure performance, and support continuous improvement initiatives.
Integration with Other Systems
Seamlessly integrating CAPA software with other quality systems, such as quality management systems (QMS) and laboratory information management systems (LIMS), to optimize workflows and data exchange.
By harnessing the power of technology, organizations can transform the CAPA process from a time-consuming, manual task into a strategic tool for driving quality and compliance.
Metrics and KPIs
Effective CAPA management requires the use of key performance indicators (KPIs) to measure performance and identify areas for improvement. Key metrics include:
- Time to Closure: Tracking the average time it takes to complete the CAPA process from initiation to closure.
- Reoccurrence Rates: Measuring the frequency of similar deviations or issues.
- Number of CAPAs by Category: Analyzing the types of deviations to identify trends and prioritize prevention efforts.
- CAPA Effectiveness: Assessing the impact of corrective and preventive actions on product quality and compliance.
- Cost of Poor Quality (COPQ): Quantifying the financial impact of quality issues and the cost savings achieved through CAPA.
- Regulatory Compliance: Tracking the number and severity of regulatory findings related to CAPA.
By monitoring these metrics, organizations can identify improvement opportunities, allocate resources effectively, and demonstrate the impact of CAPA on overall quality and compliance.
Challenges and Best Practices
Challenges
Implementing and maintaining an effective CAPA process can present several challenges:
- Resource Allocation: Balancing CAPA activities with other quality and operational priorities can be difficult, especially during periods of high workload.
- Prioritization: Determining the appropriate level of urgency for different CAPAs can be challenging, as some issues may require immediate attention while others can be addressed with lower priority.
- Root Cause Identification: Accurately pinpointing the underlying cause of a deviation can be complex, requiring thorough investigation and analysis.
- Effective Communication: Ensuring clear and timely communication among cross-functional teams involved in the CAPA process is essential for success.
Best Practices
To overcome these challenges, pharmaceutical companies should adopt the following best practices:
- Clear Roles and Responsibilities: Define roles and responsibilities for CAPA team members to ensure accountability and efficiency.
- Regular Reviews: Conduct periodic reviews of the CAPA process to identify areas for improvement and ensure alignment with organizational goals.
- Data-Driven Decision Making: Utilize data and analytics to prioritize CAPAs, track performance, and identify trends.
- Continuous Improvement: Foster a culture of continuous improvement by encouraging employees to identify and report potential issues.
- Technology Adoption: Leverage CAPA software to automate tasks, improve efficiency, and enhance data management.
- Collaboration: Foster collaboration among cross-functional teams to ensure effective CAPA implementation.
By implementing these best practices, organizations can build a robust CAPA system that drives product quality, patient safety, and regulatory compliance.
CAPA as a Strategic Tool
A good CAPA system is not just a “nice-to-have.” It’s crucial for driving continuous improvement and achieving operational excellence. By effectively managing deviations and preventing their recurrence, pharmaceutical companies can enhance product quality, mitigate risks, and build a strong reputation for compliance.
A well-executed CAPA process fosters a culture of quality and accountability throughout the organization. By embedding CAPA principles into daily operations, companies can achieve long-term success and protect patient safety.
Download our white paper, “A Step-b-Step Guide to Choosing an eQMS,” to learn more about CAPA and other key capabilities you need in your solution.