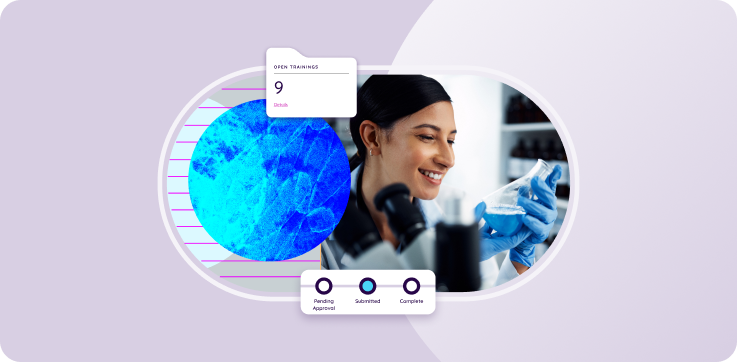
Batch Manufacturing Records (BMRs) document every step of the production process for each batch of a product. These records are essential for ensuring consistency, safety, and compliance in the pharmaceutical industry. The process of reviewing BMRs is crucial for identifying any discrepancies, addressing issues early, and ensuring that products meet quality standards before reaching the market.
In this post, we will explore the key components of a BMR, walk through the review process, and outline best practices for conducting thorough and effective reviews.
Each step in the process plays a role in maintaining compliance and preventing product recalls, making BMR review a vital part of quality assurance.
Key Components of a BMR
A typical BMR encompasses a wide range of information, including:
- Product Identification: Name, lot number, quantity produced, and expiration date.
- Raw Materials: Supplier information, quantity used, certificates of analysis, and traceability documentation.
- Production Process: Detailed steps involved, including equipment used, temperature, time, and any deviations from standard operating procedures (SOPs).
- Quality Control: Inspection results, testing data, and deviations from quality control specifications.
- Personnel: Names of individuals involved in the production process, their qualifications, and training records.
- Signatures: Signatures of authorized personnel to verify accuracy and completeness.
- Environmental Conditions: Records of temperature, humidity, and other environmental factors that could affect product quality.
- Equipment Calibration: Documentation of equipment calibration and maintenance.
Comprehensive BMR Review Process
A comprehensive BMR review process ensures that each batch of product meets required standards for quality and compliance. The review process goes beyond simply checking for completeness; it requires careful analysis to identify deviations, assess risks, and ensure that corrective actions are taken when necessary. A systematic approach to BMR review helps maintain consistency and accuracy throughout the production process, ensuring that all aspects of manufacturing are well-documented and in line with regulatory requirements.
The following section outlines the key steps involved in preparing for and conducting a thorough BMR review.
This process includes everything from gathering necessary documents and setting review objectives to detailed analysis and reporting, ensuring that every batch adheres to the highest standards of quality and safety.
Preparation and Planning
- Gather necessary documents: Collect the BMR, relevant SOPs, quality control data, and any other supporting documentation.
- Define objectives: Clearly outline the purpose of the review, such as identifying deviations, assessing compliance, or investigating complaints.
- Allocate resources: Assign qualified personnel with expertise in the specific industry and regulatory requirements.
- Establish review criteria: Develop a checklist or scoring system to ensure consistency and thoroughness in the review process.
Initial Review
- Verify completeness: Ensure that all required sections are present and filled out accurately.
- Assess accuracy: Compare the information in the BMR with the corresponding SOPs and quality control data.
- Identify deviations: Look for any discrepancies, errors, or nonconformances.
Detailed Analysis
- Investigate deviations: For each identified deviation, determine the root cause, potential impact, and corrective actions.
- Evaluate quality control data: Analyze test results, inspection reports, and other quality data to assess product quality.
- Review personnel involvement: Verify that the individuals involved in the production process have the necessary qualifications and training.
- Assess environmental conditions: Ensure that the manufacturing environment was controlled and maintained within specified limits.
- Examine equipment calibration: Verify that all equipment used was calibrated and functioning properly.
- Traceability: Ensure that the BMR provides adequate traceability to raw materials, production processes, and finished products.
Compliance Assessment
- Check against regulations: Ensure the BMR complies with relevant regulatory requirements, such as FDA, GMP, or ISO standards.
- Identify potential risks: Assess the likelihood and severity of risks associated with any deviations or nonconformances.
- Evaluate traceability: Ensure that the BMR provides adequate traceability to raw materials, production processes, and finished products.
Corrective Actions and Preventive Measures
- Implement corrective actions: Develop and implement plans to address identified deviations and prevent recurrence.
- Establish preventive measures: Implement measures to prevent similar issues in the future, such as updating SOPs or improving training.
- Document corrective actions: Maintain records of corrective actions taken and their effectiveness.
Documentation and Reporting
- Document findings: Record the results of the review, including identified deviations, corrective actions, and preventive measures.
- Prepare a comprehensive report: Generate a detailed report summarizing the review findings, recommendations, and any required follow-up actions.
- Maintain records: Store BMRs and review reports in a secure, organized manner for future reference.
Best Practices for Effective BMR Reviews
To ensure a successful BMR review process, following best practices is crucial. These practices help maintain consistency, compliance, and accuracy, while also streamlining the overall process. By establishing a structured approach and applying key principles, organizations can improve the quality of their reviews and mitigate risks more effectively.
Below are some best practices for conducting BMR reviews:
- Regular reviews: Conduct BMR reviews on a scheduled basis to ensure ongoing compliance and quality.
- Risk-based approach: Prioritize reviews based on the risk associated with different products or production processes.
- Training and education: Provide training to personnel involved in BMR reviews to enhance their knowledge and skills.
- Use of technology: Leverage software tools to streamline the review process and improve efficiency.
- Continuous improvement: Implement a system for identifying areas for improvement and making necessary changes.
- Cross-functional collaboration: Involve representatives from various departments, such as quality control, production, and regulatory affairs, to ensure a comprehensive review.
- External audits: Consider conducting external audits to provide an independent assessment of BMR review processes.
- Data analytics: Use data analytics to identify trends, patterns, and potential issues in BMR data.
- Document retention: Ensure that BMRs and related documents are retained for the required period, as specified by regulatory requirements.
Ensure Quality Through Thorough BMR Reviews
Thorough review of batch manufacturing records is essential for maintaining product quality, ensuring regulatory compliance, and protecting public health. By following the steps outlined in this guide and implementing best practices, organizations can effectively review BMRs, identify potential issues, and take proactive measures to prevent product recalls and maintain their reputation for excellence.Want to simplify your BMR review process and ensure compliance?
Request a demo today to see how our solution can help streamline your quality management and maintain regulatory standards.