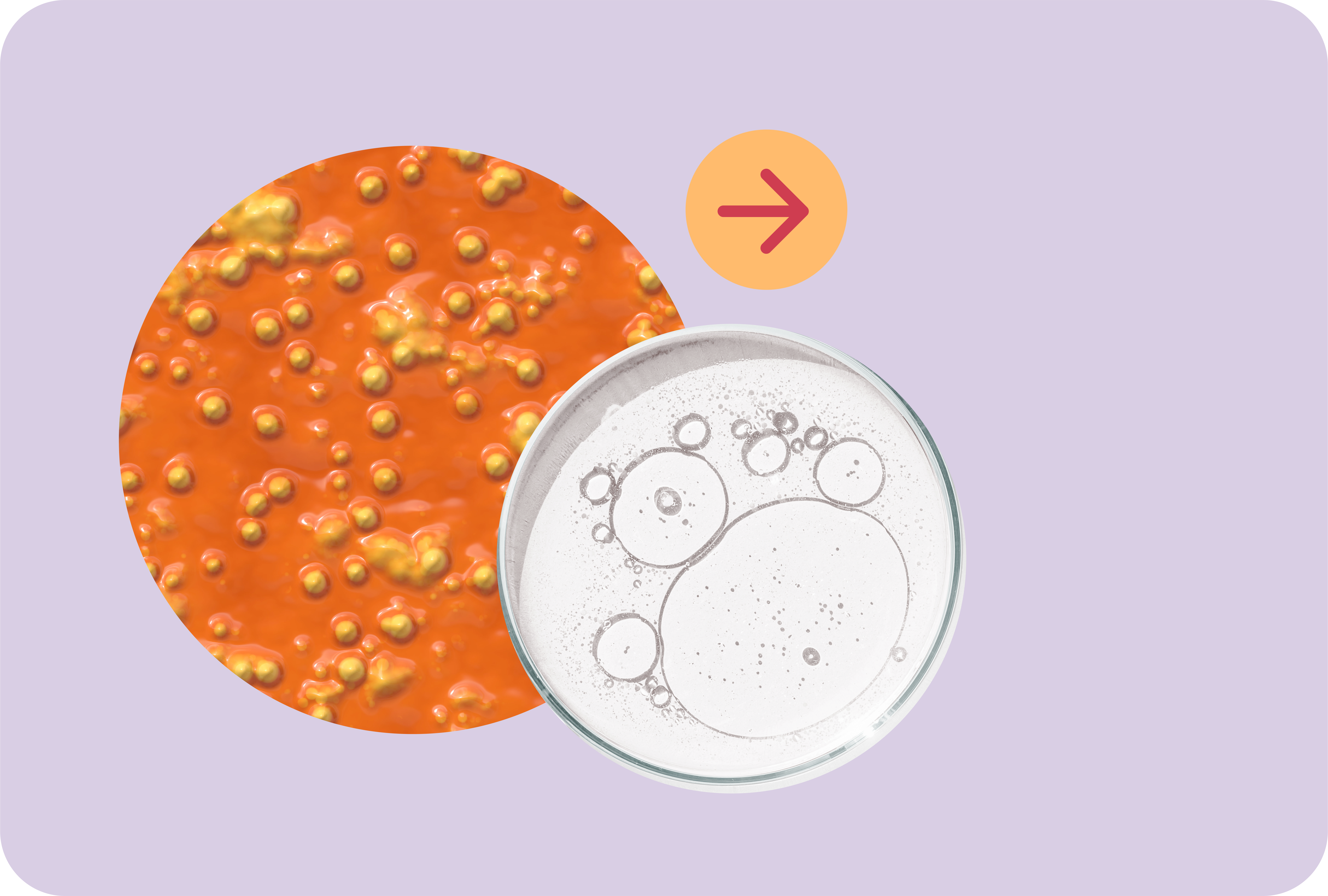
Quality management engineers in life sciences manufacturing sometimes use the terms Quality Control (QC) and Quality Assurance (QA) interchangeably. However, the two terms are quite distinct in their meaning and purpose – and are focused on different facets of the manufacturing process.
In order to apply QC and QA to the greatest effect in your quality management strategy, it’s essential to understand their specific roles and the key differences in how they impact your business processes.
What Is Quality Control?
Quality Control is the process of inspection, testing, and approval that ensures products meet customers’ requirements and the applicable regulatory standards. It plays a critical role in the manufacturing process because it prevents defects from reaching customers and ensures that each customer will receive the same quality product every time.
In pharmaceutical and medical device manufacturing, effective quality control procedures are therefore of the highest importance. This is because of the potential harm and safety risks that can arise from using a defective product in a healthcare setting.
Strict quality control measures need to be in place at each stage of manufacture and, most importantly, at the end of the manufacturing process. At the final stage, tests need to be applied against predetermined acceptance criteria to verify that the finished products meet all applicable quality and regulatory standards.
What Is Quality Assurance?
Whereas quality control focuses on testing to ensure that your product is safe and effective for use, Quality Assurance is the process of building that quality into the product.
Quality control can be thought of as reactive because it tests to ensure the manufacturing processes have produced a product of the required quality. In contrast, quality assurance is proactive, shaping and fine-tuning the manufacturing processes to prevent defects.
If QC testing finds defects, it is the role of QA to go back, re-evaluate, and then re-design the manufacturing processes. QA makes corrections and improvements to prevent those defects from occurring. QA and QC are, therefore, two sides of the same coin.
Rigorous quality assurance and quality control are vital to ensure your products’ safety and compliance. They are essential for compliance with the ever more stringent measures required by regulatory agencies to protect against contamination, tampering, or errors in life sciences manufacturing.
Vital Distinctions Between QA and QC
So far, we have sketched out definitions of quality assurance (QA) and quality control (QC). We’ve seen the vital but different role each plays in ensuring the safety and compliance of the products leaving your manufacturing facility. Now we’ll investigate the key differences between QA and QC to demonstrate how each makes a distinct contribution to the high levels of quality management required in life sciences manufacturing.
Who Is Responsible for QA and QC?
The Quality Management System (QMS), including specification of the quality assurance systems and processes, is generally the responsibility of a dedicated quality assurance unit and the organization’s leadership team.
However, QA embraces the actions of every member of a life sciences organization. All staff are responsible for following the standard operating procedures (SOPs) specified by QA to ensure a consistent, reliable, high-quality outcome.
QC, by contrast, generally involves the specific quality control personnel only, who are solely responsible for product testing and process validation.
Which Areas of the Manufacturing Process Do QA and QC Focus On?
Quality assurance systems and processes are the methods and procedures used to protect and preserve quality standards. QA is about system processes, such as documentation, audits, personnel training, and change control.
Quality control, by contrast, carries out moment-in-time measurements and verification of parts. This includes raw materials from a supplier and the final products created via the manufacturing process. QC procedures include batch inspection, product sampling, laboratory testing.
What Are the Specific Roles of QA and QC?
Quality Assurance’s role is to design processes and specifications that ensure the manufacture of high-quality products that meet regulatory requirements and also customers’ needs and expectations. As such, QA is focused on the prevention of inconsistencies and defects.
QA processes include Document Management, Audits, Supplier Management, Training, Change Control, and Deviations.
The function of QA must be independent of manufacturing and operations so that the focus is rigorously on quality assurance and the elimination of process variation. This focus is achieved through explicitly defined procedures (by QA), followed precisely by manufacturing and operations.
QA teams also serve vital post-production roles in implementing process improvements whenever possible. They also lead the investigation and correction of any quality issues identified by QC. The investigation of potential root causes of a quality issue is a further reason why the independence of the QA team is critical.
Quality Control is not focused on the process of manufacturing. Instead, its role is to create and employ procedures that identify quality issues in the resulting product created through the actions and processes specified by QA.
QC procedures include Batch Inspection, Laboratory Testing, Product Sampling, and Validation Testing.
Where in the Manufacturing Process Are QA and QC Employed?
QA creates the framework for ensuring customers receive products of the highest quality as needed. As such, it is involved in the creation of a product. It achieves this goal by defining the standards and protocols for products at every stage of production and distribution, from design and manufacture to packaging, marketing, and sales.
QC provides the ‘gate’ of inspection and testing to verify the safety and efficacy of products. It is employed to certify verification that QA systems and processes have succeeded in ensuring product quality – so that only safe, high-quality products without defects reach the customer.
How Do QA and QC React When Utilized in Manufacturing?
As we have seen above, the role of QC is to measure and test products and processes against the established specifications to verify that they consistently meet the required regulatory and quality standards. As such, QC is reactive – inspecting, testing, and verifying the results of a manufacturing process.
QA, by contract, is focused on process design, such as documenting standard operating procedures (SOPs), to ensure consistent product quality and prevent defects before they occur. In this way, QA is proactive.
Integrating QA and QC Within an Overall Quality Management System
The regulatory landscape of the life sciences industry is continuously expanding – as well as becoming more competitive. Continuous improvement is as essential as regulatory compliance. Both QA and QC are absolutely necessary for compliant manufacturing in the life sciences industry. But integrating both within a rigorous, data-driven Quality Management System (QMS) provides the opportunity for end-to-end quality management throughout the product value chain.
Utilizing QMS allows pharmaceutical and medical device manufacturers to mitigate risks while creating visibility and traceability from the beginning of the design cycle through manufacturing and post-market monitoring. Automating quality processes while continuously monitoring, tracking, and reporting on regulatory requirements not only makes your business compliant but also helps to ensure fewer defects and inconsistencies.
Crucially, an efficient QMS also opens the door to quality-first thinking across the organization and continuous improvement throughout the design and manufacturing processes.
Conclusion
For life sciences manufacturers, successful implementation and coordination of Quality Assurance and Quality Control are crucial to success. Creating processes that result in a consistent flow of high-quality, defect-free products results in a win for all stakeholders. Managing QA and QC within a seamless QMS ensures that processes and products are subject to comprehensive management with positive outcomes.