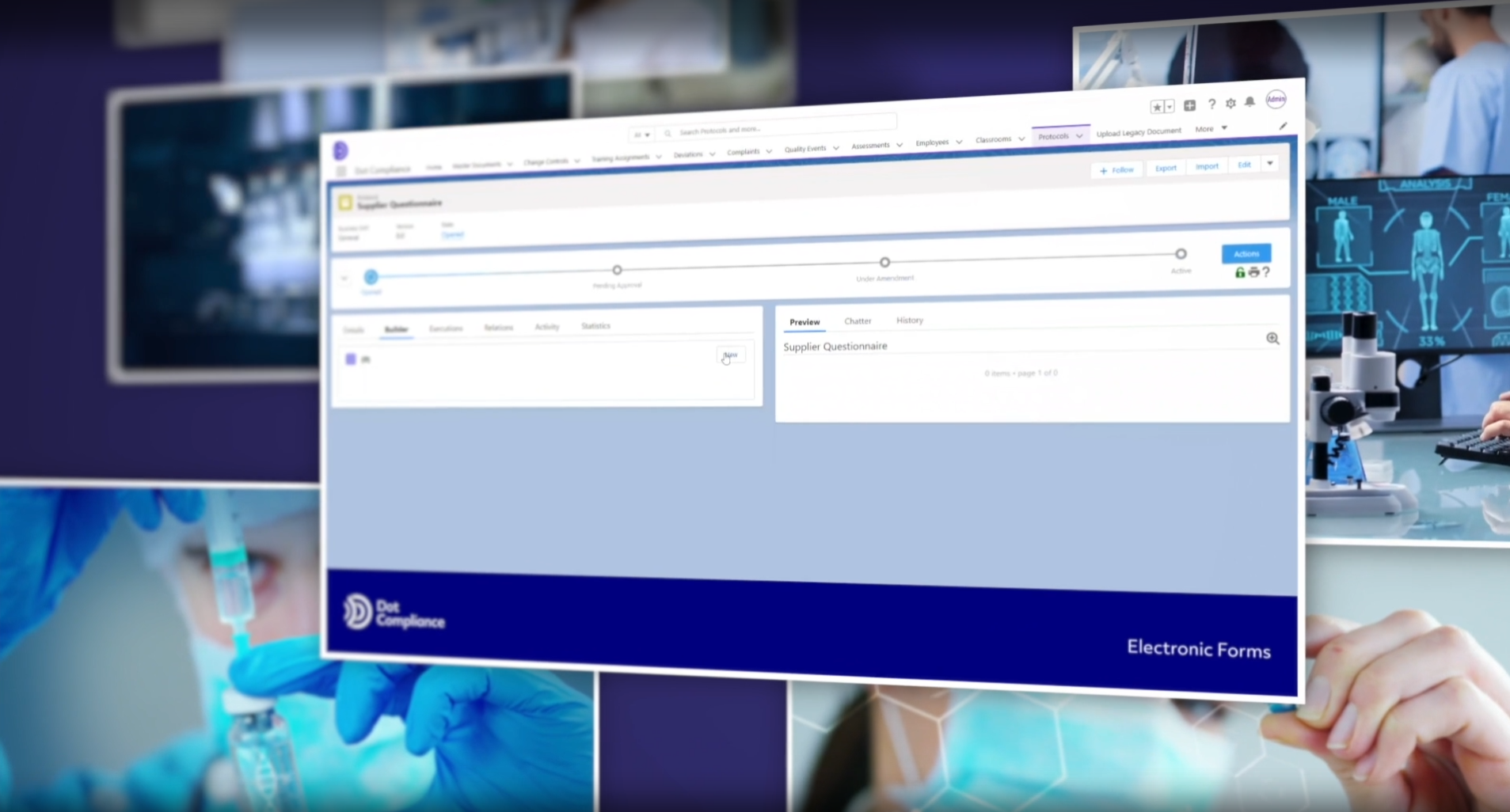
Electronic Forms: Create validated electronic forms on demand.
There are obvious benefits derived when transitioning from manual processes or on-premise systems to an electronic, automated quality management system (QMS) in the cloud. Benefits range from process efficiency, flexibility, accuracy and greater access to data and analytics. In a survey of life science companies by KPMG, 64% cited cloud technology as one of their top priorities in enhancing internal efficiency.
So, it’s a known fact that digitized quality and compliance processes are the critical engines that support life science manufacturing. Yet, an often overlooked aspect of automated process management is the importance of electronic forms. No matter how large or small a company is, as the organization grows and products are developed and needs evolve, quality teams must generate new forms to meet compliance goals and regulatory requirements. Leveraging the capabilities of electronic forms in a cloud-based QMS, can help quality oversight in life sciences manufacturing by adding critical data to records, without having to generate required fields and revalidate their QMS. Take for instance a checklist for an investigation or another form related to a process that isn’t inherently in the QMS.
Some examples include:
- On-boarding new employees
- Auditors’ checklist for internal / external audits
- Vendors / suppliers / CMOs qualification questionnaire
- Temp / humidity monitoring
- Logbook (handover) management
- Cleaning execution / verification for facility / equipment
In a conventional QMS environment, quality professionals don’t have the capabilities to generate these forms themselves. Instead, they have to rely on the vendor, a team of developers or consultants to generate the form and validate it, which takes time and money.
With a fully validated, pre-configured, ready to use QMS, the quality team can generate the forms they need themselves, when they need them, using a tool that is part of the solution. They simply create the necessary form, which itself is validated. With no third-party intervention required, the quality team quickly has what it needs in hand at no added cost.
Let’s dive into a complaint handling use case where the company has a product complaint and must determine whether it needs to report the complaint to a regulator. There are a series of questions every company must answer to determine if a complaint is reportable (e.g., was there an adverse event, did it involve the product, what countries does this impact, etc.).
The quality team can use the tool within DOT Compliance QMS to create a form with a defined set of questions from the quality team, relevant to that product and compliance requirements. It can even include a decision tree to guide them through questions for comprehensive but rapid decision making.
How about the ever-expanding life sciences supply chain, extending to suppliers throughout the world? Having validated electronic forms on demand can enable a company to assess its supplier operations quickly and effectively.
For example, a company can generate a survey to determine if its suppliers are maintaining compliance from a product perspective, send it to suppliers electronically, and ask to receive it back electronically with documents attached to confirm their compliance status. Everything comes back into the QMS and the task is marked complete. Again, because the survey was generated through a tool integrated into the QMS it’s already validated. Electronic forms used in this way facilitate visibility and connectedness for quality outside of the organization’s four walls.
There are so many ways to leverage the electronic forms in a QMS solution if you have the right one in place. Wouldn’t it be great to share electronic form templates with others in the field and foster best practices throughout the industry? The future goal is to create industry standard templates for specific use cases that all users of the QMS platform can access within the solution. In this way life science companies can leverage resources that have been proven effective instead of having to create their own. The power of electronic forms is truly endless.